ISO 8573 Compressed Air Testing
Our AirCheck✓™ Team of Experts is only a few clicks away. Trace Analytics is your lab for compressed air testing per ISO 8573. Contact us via our website and our team will respond quickly to your needs.
Compressed Air Testing to ISO 8573
More than 70% of production facilities use compressed air in the manufacturing process.
If the compressed air becomes contaminated, it will adversely affect the quality of the product. Proper assessment of the compressed air system, and regular testing can prevent serious contamination and promote the overall health of the system. Test your compressed air to ISO 8573 to ensure that compressed air is not a source of contamination is essential to producing a high-quality product.
ISO 8573 Contaminants: What To Test For
Manufacturing Industries Served
More than 70% of production facilities use compressed air in the manufacturing process. Proper assessment of the compressed air system, and regular testing can prevent serious contamination and promote the overall health of the system. ISO 8573 compressed air testing is a great way to ensure your system is producing quality, safe compressed air.
Pharma & Med Device
Process air and gas testing available to meet ISPE requirements. ISO 8573, 14644, and custom specs are available for testing particles, water, total oil and microorganisms.
Nuclear
Test instrument air to ANSI/ISA S7.0.01-1996. Clean, dry air for pneumatic instruments addresses dewpoint, particle size, lubricant, and contaminants.
How to Test: ISO 8573 AirCheck Kits for Compressed Air
ISO 8573 is an internationally recognized standard that defines major contaminants in compressed air and presents a comprehensive system for air purity designations. The implementation of this standard supports accurate testing of the major contaminants in compressed air – particles, water, oil, and microorganisms. ISO 8573 is used widely throughout the compressed air industry, acting as a common language available to the manufacturer, compressed air system supplier, and compressed air testing laboratory.
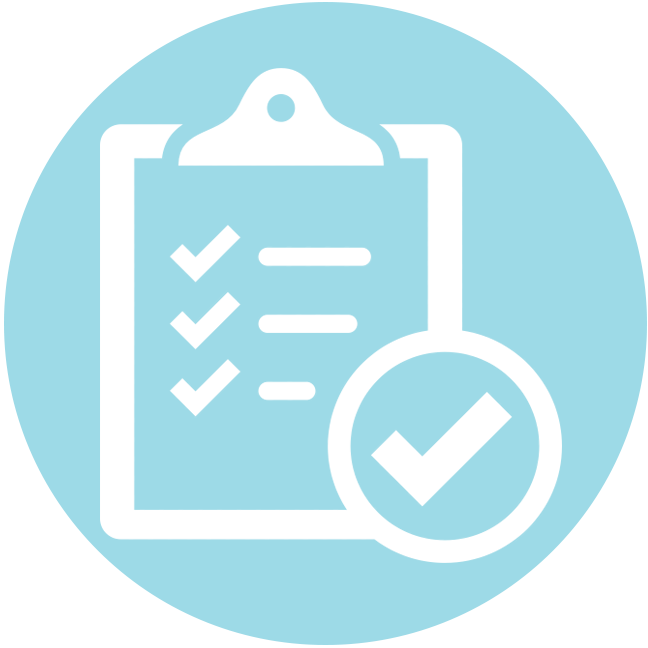
Analytical methods and sampling techniques
- Laser Particle Counter
- Microscopy
- Detector tubes
- Gas chromatography
- Gravimetry
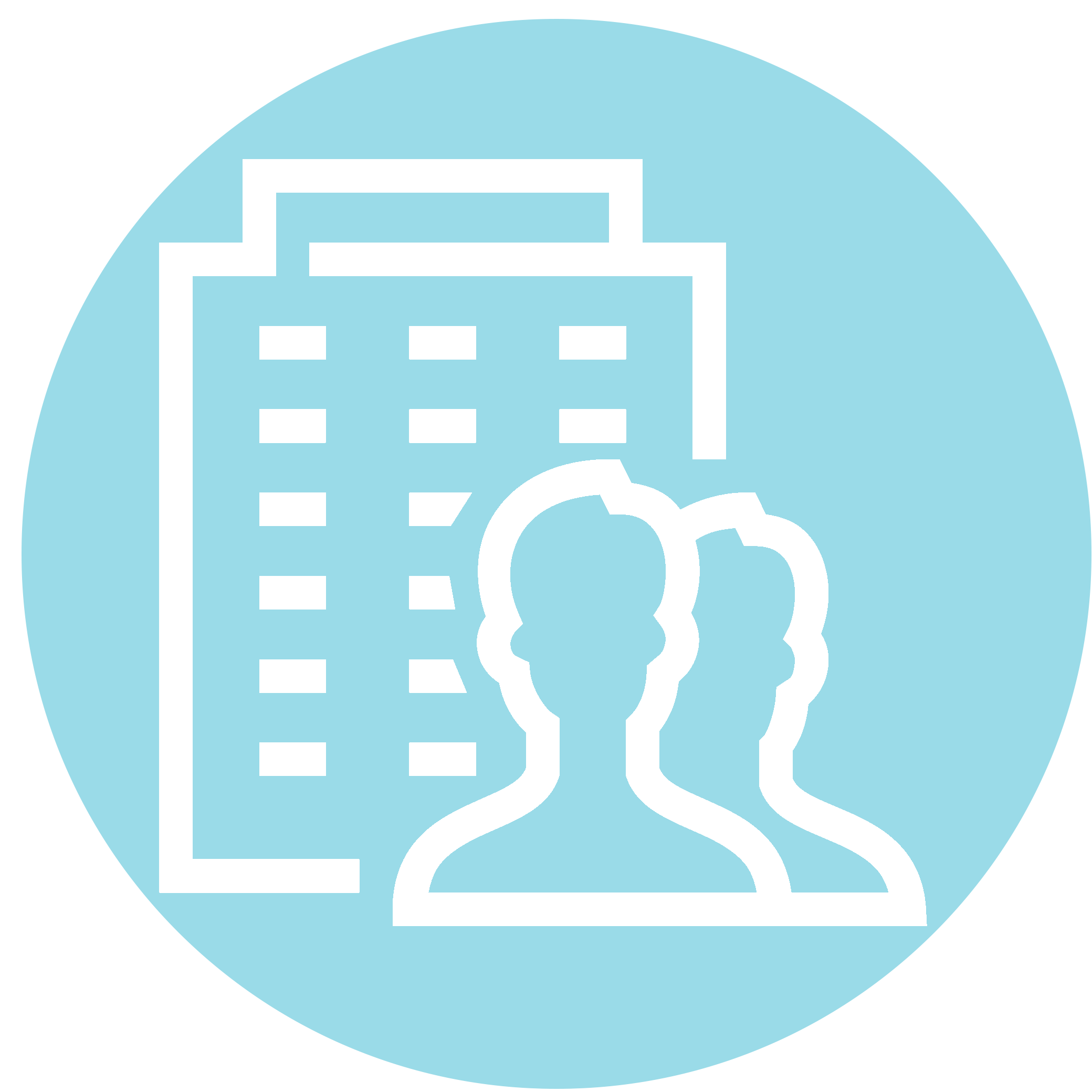
Align with compressor and filtration capabilities
- Atlas Copco
- CompAir
- Kaeser
- Parker Hannifin
- Sullair
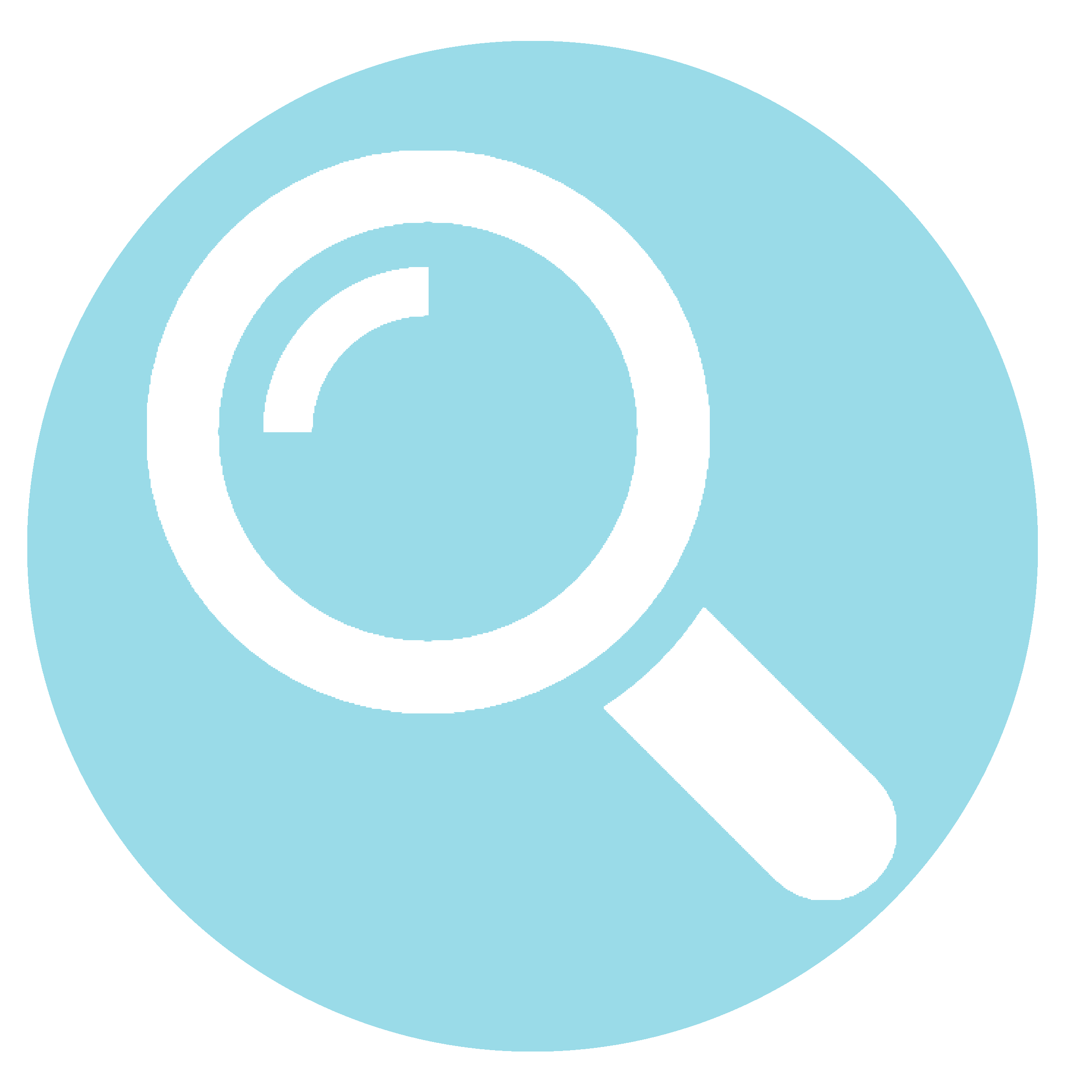
Comprehensive purity designations
- Particle Classes 1–9
- Water Classes 1–6
- Oil Classes 1–4
- Custom specs available
K810 AirCheck Kit
The AirCheck✓ Kit™ K810 is designed to met ISO 8573 compressed air purity classes for manufacturing facilities. Custom specifications are available.. This kit is typically used by food, pharmaceutical, medical device, and nuclear customers who use low pressure compressed air systems in their processes. Test from the compressor or point of use. Watch our online sampling video for Manufacturing Air Testing.
ISO 8573-1 Purity Classes
ISO 8573-1:2010 COMPRESSED AIR CONTAMINANTS AND PURITY CLASSES | ||||||||
---|---|---|---|---|---|---|---|---|
CLASS | PARTICLES | WATER | OIL | |||||
By Particle Size (maximum number of particles per m3) See Note 2 |
By Mass | Vapor Pressure Dewpoint | Liquid | Liquid, Aerosol, & Vapor See Note 1 |
||||
0.1 µm < d ≤ 0.5 µm | 0.5 µ m< d ≤ 1.0 µm | 1.0 µm < d ≤ 5.0 µm | mg/m3 | °C | °F | g/m3 | mg/m3 | |
0 | As specified by the equipment user or supplier and more stringent than class 1 | |||||||
1 | ≤ 20,000 | ≤ 400 | ≤ 10 | - | ≤ -70 | ≤ -94 | - | ≤ 0.01 |
2 | ≤ 400,000 | ≤ 6,000 | ≤ 100 | - | ≤ -40 | ≤ -40 | - | ≤ 0.1 |
3 | - | ≤ 90,000 | ≤ 1,000 | - | ≤ -20 | ≤ - 4 | - | ≤ 1 |
4 | - | - | ≤ 10,000 | - | ≤ +3 | ≤ +37 | - | ≤ 5 |
5 | - | - | ≤ 100,000 | - | ≤ +7 | ≤ +45 | - | - |
6 | - | - | - | 0 – ≤ 5 | ≤ +10 | ≤ +50 | - | - |
7 | - | - | - | 5 – ≤ 10 | - | - | ≤ 0.5 | - |
8 | - | - | - | - | - | - | ≤ 5 | - |
9 | - | - | - | - | - | - | ≤ 10 | - |
X | - | - | - | > 10 | - | - | > 10 | > 5 |
MICROBIOLOGICAL CONTAMINANTS | OTHER GASEOUS CONTAMINANTS | |||||||
No purity classes are identified | No purity classes are identified Gases mentioned are: CO, CO2, SO2, NOX, Hydrocarbons in the range of C1 to C5 |
|||||||
Note 1: ISO 8573 Oil includes aerosol, vapor in the range of C6+, and liquid oil. Liquid oil is typically sampled when wall flow is present, contamination is suspected, or results are greater than 5 mg/m3. Trace can provide a separate kit for liquid oil testing. Note 2: For Particle Class 0, 1, & 2 (0.1 - 0.5 µ range only), a laser particle counter with a high-pressure diffuser is required. Rental of this equipment is available on a reservation basis. Contact us for details. To qualify for Particle Classes 0 through 5, there can be no particles greater than 5µ present. In some cases, Trace uses alternative sampling techniques or analytical methods to those specified in ISO 8573, for details see Smith White Paper, 2012. |
||||||||
Air & Gas Specifications referenced above may be viewed and/or purchased from: ANSI - American National Standards Institute |
Industries We Serve
Why Choose Trace Analytics?
Accredited
Our A2LA accredited laboratory is an unbiased third-party laboratory with no financial interest in other compressed air products. The extensive quality control procedures at Trace’s lab ensures that you will receive quality data. Trace is an A2LA accredited laboratory complying with ISO 17025, certificate #0322-01.
Easy to Use Kits
The AirCheck✓ Kit™ is designed for use with compressed breathing air specifications requiring a dry dew point, such as ISO 8573, NFPA 1989, CGA, ISPE, and more. Other specifications are available. These kits are typically used by food, packaging, medical device, pharmaceutical, nuclear, scuba divers, fire departments and industrial breathing air facilities to test compressed air to meet their requirements.
Satisfaction
Compressed air has been our specialty since 1989 — our AirCheck✓™ Team of Experts has decades of experience in the specific field of compressed air and environmental analyses, testing, and troubleshooting. Excellent customer service, and the desire to provide a more efficient and accurate testing experience, have been the backbone of our company since 1989 — and still hold true today. We pride ourselves on the level of customer service we provide — it is the core of our relationship with all of our customers.
Other Testing Services for Manufacturers
TOLL FREE
1.800.247.1024
LOCAL LINE
512.263.0000
OFFICE HOURS (CT)