In order for manufacturers to ensure the safety of their end-products, a compressed air monitoring plan must be established. By determining a specific goal that assesses their risks and meets necessary regulations, manufacturers can achieve and maintain quality compressed air systems.
Hazards that Affect Compressed Air Systems
Each facility faces unique hazards and risks. These can come from a variety of sources which can be difficult to pinpoint as compressed air systems are generally complicated, especially in large facilities. Contamination can enter systems through the intake air, due to inadequate filtration, inappropriate piping, or even seasonal changes. According to ISO 8573, particles, water, oil, and microorganisms are all contaminants that can negatively impact products and put consumers at risk.
Create a Risk Assessment
Manufacturers must carefully assess the risks associated with particles, water vapor, oil, gas, and microbial contamination. Any compressor contamination could risk the safety of their end-products and users. For this reason, it is important to identify hazard types, the level of harm that they can cause, and the probability of these hazards to occur.
Determine Which Regulations to Follow
The following organizations include various guidelines for proper compressed air testing and system monitoring:
- International Standard for Organization (ISO)
- Compressed Air and Gas Institute (CAGI)
- British Retail Consortium (BRC)
- Safe Quality Food Institute (SQF)
- Food & Drug Administration (FDA)
- Food Safety Modernization Act (FSMA) – Implemented by the FDA to clarify necessary actions to protect consumers from food-borne illnesses
- Hazard Analysis and Critical Control Point (HACCP) – Used by BRC to ensure and control the biological, chemical, and physical hazards that can be associated with a food manufacturing system
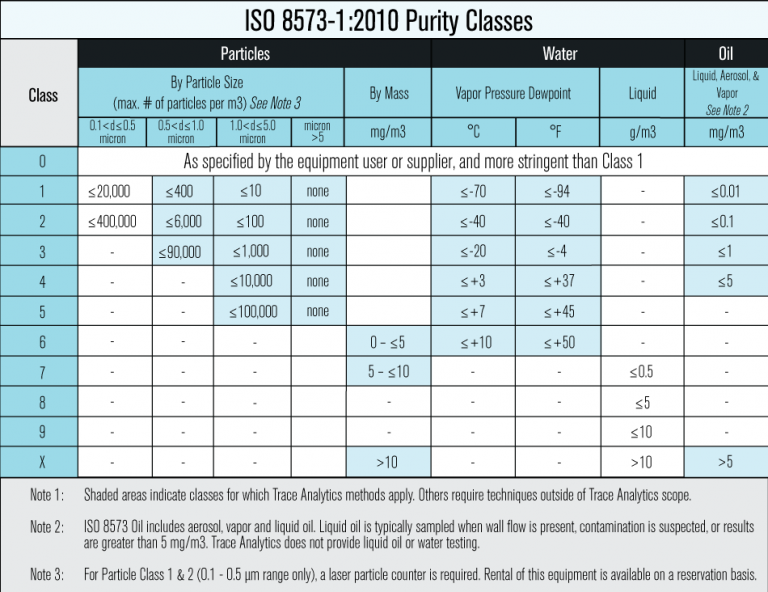
Consequences of a Contaminated Compressed Air System
Compressed air contamination can cause manufacturers substantial costs, loss of productivity, and serious risks to consumers. For example, a systemic leak could end up costing a company around $20,000 (Kaeser Compressors, 2007). In 2001, a fortune 500 company recalled a contaminated product which resulted in a $2 million potential profit loss (Sterling, 2011).
Lack of regular compressed air testing can result in failure to determine the date, location, and extent of contamination.
Setting a Compressed Air Monitoring Goal
The first step to satisfy requirements and ensure system health is to decide which compressed air monitoring plan best suits their particular needs. For example, some companies may only test once per year in order to satisfy SQF requirements, while others may want to know whether there is compressed air quality degradation present and at which sampling point it occurred. Additionally, many companies choose to test several times a year to understand how maintenance and seasonal changes affect their systems.
How to Establish a Compressed Air Monitoring Plan
- Take stock of all pieces
- Create a risk assessment
- Create a diagram of your system
- Document maintenance performed
- Test your compressed air regularly with an A2LA accredited laboratory
- Analyze data points
Ultimately, a company’s regulations, location, and end-product will determine their individual compressed air testing goals. Manufacturers meeting their compressed air monitoring goals helps to ensure product safety.
For more information, please contact us.
Original article published on International Food Safety and Quality Network.